Founder Mitja Hinderks, working with a team, has come up with a series of innovations to cut greenhouse gas emissions, all of which would lead to major energy savings. The key innovation is the development of uncooled internal combustion engines (ICEs) for all applications and fuels.
There are three other significant groups of innovations in the areas of: Continuously Variable Transmissions (CVTs); Commercial Hydrofoil & other Marine Craft; Hybrid-Drive & other Aircraft.
Uncooled Internal Combustion Engines (ICEs)
Between 35% and 40% of man-made CO2 comes from all ICEs used in vehicles, ships, electricity generation, rail and industrial / agricultural equipment. Today, piston engines dissipate (waste) 30% to 60% of fuel energy via air- or water-based cooling systems and general radiation. This is unsustainable.
Uncooled internal combustion engines are for applications in every industry and for all current fuels, including clean fuels such as hydrogen and ammonia. Compared to today’s cooled engines, they would have about three times the efficiency (using one third the fuel); be many times smaller and lighter; virtually silent; simpler and more reliable because they would have far fewer moving parts; have no cooling or piston / cylinder oil systems to fail nor toxic fluids to dispose of. They would reduce CO2 emissions by around two-thirds, greatly reduce emissions of particulates and NOx so improving health wherever used. Much lighter engines and less-needed fuel will provide longer operating ranges for cars, heavy goods vehicles (HGVs), rail, ships and aircraft, providing further efficiency gains.
It will be a long time before green fuels such as hydrogen and ammonia and their infrastructures will be widely available. Today, there are few alternatives to fossil fuel use for ICEs in heavy vehicles; rail; shipping; aircraft; mining, and agricultural / industrial equipment. Nearly all these applications are switching to hybrid drives, which need no new infrastructure, use far less batteries, and are for all countries and terrain. Only some light vehicles could be all-electric. With their charging systems and added electricity generating requirements, they are mostly not affordable or practical in many less-developed countries. ICEs must be made more efficient.
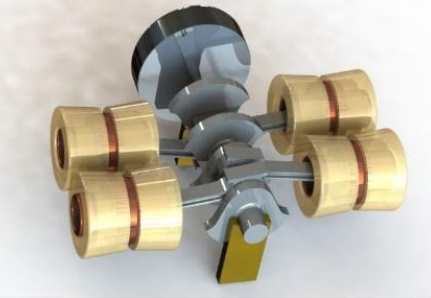
Uncooled engines will run at very high pressures and temperatures, enabling more fuel energy to push the piston (according to the Carnot rule), with the rest held in the much hotter exhaust gas where it can be retrieved to do more mechanical work and increase performance, using current exhaust heat energy recovery technology. Because of the high temperatures, the traditional piston / cylinder oil system is not usable. Instead, the components are separated by gas bearings, a well-known technology.
Pistons and cylinders of industrial ceramic are in heavily thermally and acoustically insulating casings. Typically, an electrical generator would be coupled to the engine inside the casing to make a gen-set. With no plumbing for cooling or for piston-cylinder oil systems, engines can be ’snap-in’ cartridges. Equipment no longer needs to be towed to a repair facility; engines can be replaced onsite, a game changer. Litus has solved earlier problems on use of ceramics in engines.
recess in equipment
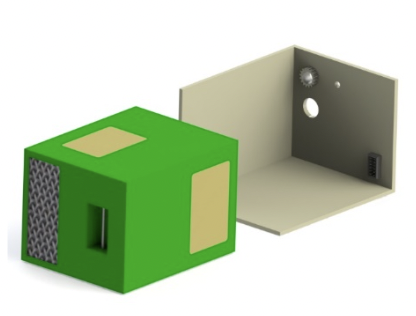
engine module
Efficiencies for uncooled engines of all size ranges will be between 47% and 52%, without using an exhaust heat energy recovery system (EHERS). In contrast, smaller engines today have real-world efficiencies of 5% – 15%, with larger ones – often using some exhaust energy – generally having real-world efficiencies in the 25% – 40% range. Adding EHERS to uncooled engines can boost efficiencies to the circa 75%-plus region, depending on number and type of EHERSs used. Multiple EHERSs are practical in rail, marine and stationary engine applications.
A commercialization Alliance is being established. It is planned to be incorporated as a stock-issuing entity by this November, when Litus will transfer the engine project together with its IP and the development team to it. Alliance participants will include financial partners, research institutions, large users of engines, component manufacturers, government agencies and others. Contact us for more information.
Litus is seemingly alone in working on uncooled engines; they do not exist anywhere yet. It is one of the few projects that could quickly cut emissions and slow warming. Once available, uncooled engines – with their many advantages including halved fuel costs – could almost completely replace today’s cooled engines, cutting global man-made CO2 by roughly 20% within a decade or so, by over 30% if largely using hydrogen and / or ammonia. In 2017 the global piston engine market was worth $ 670 Billion. It would be much more during a transition to uncooled engines.
A 7-page illustrated description of a key version of the Litus uncooled engine is available.
Important Applications
Uncooled engines are a least twice as efficient, many times smaller / lighter and – importantly – virtually silent, compared to conventional cooled engines. The weight savings of engine and needed fuel extends range and / or payload. The small, light engines or gen-sets can be snap-in units, making them far easier to instal and maintain on all equipment, including such as such as oilrigs, combine harvesters, ships, etc. For military applications, there need be no significant heat signature. Exhaust can be ducted or diluted, before leaving the item of equipment.
Heavy Vehicles / Industrial & Agricultural Equipment
All-electric drives are rarely viable for these applications, because of the extra weight of the battery pack, its support structure and the extra energy needed to drive / accelerate them. There is often no charging infrastructure. Today, engine noise is usually problematic. Using snap-in modules, equipment can be serviced in the field, rather than transported to an often remote repair shop.
Marine Craft
For most medium to larger size craft all electric is not an option, except for short ferry crossings. Multiple small light silent uncooled engines / gensets would replace single large slow-running cathedral engines and could be mounted in almost any position on / in a ship. Noise is problematic for most marine creatures. The lightened engine and fuel would let the craft ride higher, leading to reduced water resistance and further energy savings. Snap-in units could be easily removed / replaced, almost impossible with today’s large engines. Multiple drives provide important safety margins; if one fails the craft is still mobile. With large single-engine failures, the craft is dead in the water.
Aircraft, including Helicopters, Airships and Blimps
For all except a few specialist applications, all-battery drives are not considered viable. Instead, hybrid drives are being developed, often with only a small load-levelling battery pack, mostly for extra power during take-off. Super light, small and silent gensets can be located within the aircraft (where they can be got at during flight) and wired to propellers, fans or turbines mounted on the wings or exterior of the fuselage. Depending on power output, the engines would weigh between a quarter and a tenth of ICEs or turbines. They would be nearly silent. Twice as efficient, reductions in weight and needed fuel would allow for increased payload and / or range.
Self-propelled Military Equipment & Military Gen-sets
Combustion engines are used in a wide range of equipment, including landing craft, torpedoes, tanks, troop carriers etc, as well as to power air-conditioning and heat-pumps. Greatly superior power density would give mobile equipment increased speed and range. If the equipment used half the fuel, logistics requirements and costs are seriously cut, exposing less personal to the danger of getting fuel to the operations zones, with near silence / lack of heat signature reducing risk of detection.
Non-electrified Rail
In most regions, apart from commuter rail, there is no installed base of electrified long-distance track; trains are powered by combustion engines, as in the USA, India, Asia, Australia, Africa, Latin America, Russia, and large parts of Europe. Providing electric power for high-speed rail (HSR) track is a large portion of total electric HSR system costs, especially when power supply infrastructure has to be installed in remote and often desert regions. Electrification adds to security and safety concerns, since pylons and power lines are more susceptible to damage and sabotage than track.
Alternatives are trains powered by super-efficient virtually silent un-cooled engines / gensets having between five- and ten-times better power-to-weight and -bulk ratios than current engines. Diesel and gaseous fuels including hydrogen can be used. They would consume less energy, cost less, and emit less pollutants than an equivalent all-electric powered train, if generating and line transmission in-efficiencies were taken into account, as well as the energy and pollution costs of constructing an electrical supply system. Depending on prevailing fossil fuel costs, running uncooled IC engines could be cheaper than running on overhead electricity. More information on rail applications is available.
Gen-sets & Emergency Gen-sets
For the construction industry and for stand-by power applications (hospitals, high-rise building elevators, airport control towers, etc), much smaller, lighter, doubled- efficiency and virtually silent gen-sets would provide enormous benefits. The up to ten times greater power density of uncooled gensets would make local or international rescue efforts – such as for the recent Turkish / Syrian earthquakes – quicker and easier. A gen-set of 1.5 MW could be mounted on a pick-up truck or easily air-lifted; a class 8 truck could house a 16 MW gen-set (enough to power a large ship).